The Importance of Sensors in Modern Robotic Systems
- Macy Mo
- Apr 1
- 4 min read
Robotics is a rapidly evolving field that combines advanced technology with practical applications across various industries. A crucial element in the operation of modern robotic systems is the integration of sensors. These devices allow robots to perceive their environment, make decisions, and act accordingly, often in real time. As we delve into the various aspects of sensors in robotics, we'll explore their significance, types, and the future of sensor integration.
Understanding Sensor Integration in Robotics
Sensor integration refers to the process of incorporating diverse sensors into robotic systems to enhance their functionality. This integration is essential as it allows robots to gather data, analyze information, and respond to surrounding conditions. Without sensors, robots would operate blindly, lacking the ability to interact safely and efficiently within their environments.
For example, in industrial settings, sensors can monitor the operational status of machines and detect potential failures before they lead to costly downtime. Similarly, in autonomous vehicles, sensor integration helps in navigating complex road conditions while ensuring passenger safety.
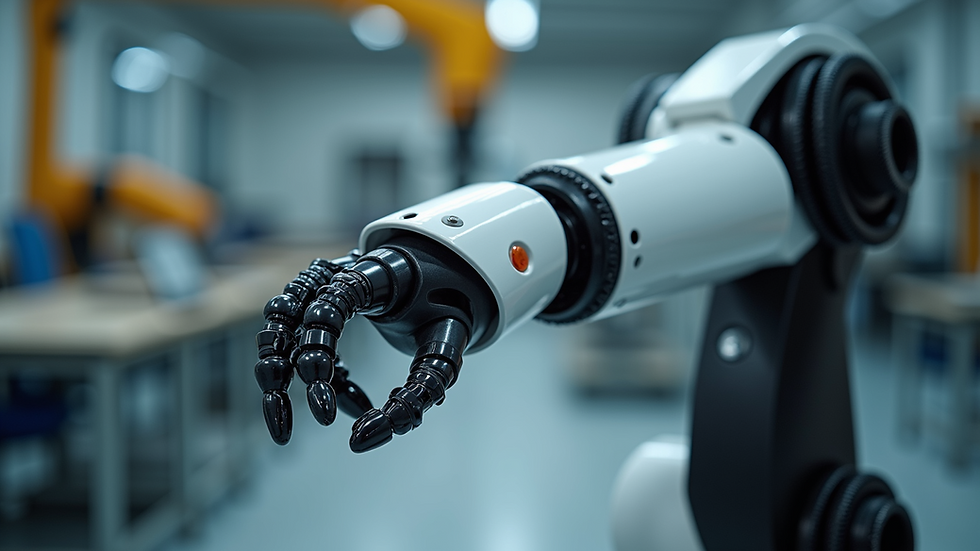
Types of Sensors in Robotics
Robotics employs a wide range of sensors, each serving a unique purpose to improve robot functionality. Let’s take a closer look at some of the most prevalent types of sensors used in robotic systems today.
What are the 4 Sensors in Robotics?
Proximity Sensors: These sensors detect the presence of nearby objects without physical contact. They are often used in robotics for collision avoidance, ensuring that robots can navigate around obstacles safely. Infrared and ultrasonic sensors are common examples of proximity sensors.
Camera Sensors: Visual perception in robots is achieved through camera sensors. They allow robots to "see" and interpret their environment, which is critical for tasks ranging from object detection to facial recognition. This capability is particularly important in fields like security and surveillance.
Gyroscope Sensors: Gyroscopes are used to measure and maintain orientation based on angular momentum. In robotics, they help in stabilizing movement and maintaining balance, which is essential for both aerial and ground-based robots.
Temperature Sensors: These sensors measure the ambient temperature and are vital for robots operating in environments where temperature control is essential, such as in food processing or manufacturing.

How Sensors Improve Robotics Performance
The integration of sensors significantly improves the performance of robotic systems in various ways. Here are some noteworthy benefits:
Enhanced Decision Making
By providing real-time data, sensors allow robots to make informed decisions swiftly. For example, autonomous drones equipped with visual and temperature sensors can assess a situation and decide their next step, such as changing altitude or adjusting speed based on environmental conditions.
Increased Efficiency
Sensors contribute to the efficiency of robotic systems by minimizing errors and optimizing performance. In manufacturing, robots equipped with pressure sensors can adjust force applied during assembly tasks, which prevents damage and ensures quality, thereby streamlining production processes.
Safety and Precision
One of the paramount advantages of using sensors in robotics is the enhancement of safety and precision. Robots integrated with collision-detection sensors can maneuver around people and obstacles without causing harm, making them suitable for deployment in crowded environments such as hospitals or warehouses.
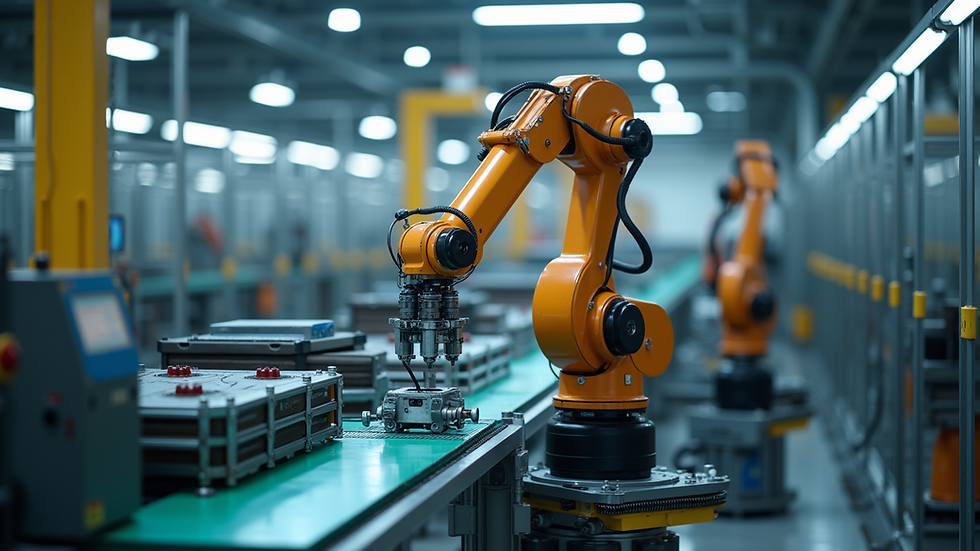
The Future of Sensor Integration in Robotics
As technology evolves, so does the potential for sensor integration in robotics. Several emerging trends are expected to shape the future of robotics, enhancing capabilities and functionalities.
Advanced Sensor Technologies
With advancements in sensor technology, we can expect more sophisticated sensors that offer increased accuracy and reliability. For instance, the development of multi-sensor systems, where a single robot can utilize various sensors simultaneously, will greatly improve the robot's adaptability to different environments.
Integration with AI and Machine Learning
The combination of sensors with artificial intelligence (AI) and machine learning will take robotic capabilities to new heights. AI can analyze the vast amounts of data collected by sensors and continuously improve robotic functions. This integration allows robots to learn from past experiences, enabling them to perform tasks with increased efficiency over time.
Expansion into New Industries
The demand for robotics is growing across sectors such as agriculture, healthcare, and logistics. As sensor technology continues to improve, we can anticipate greater adoption of robotic systems in these areas. For example, in agriculture, robots equipped with soil moisture and temperature sensors can determine the best times for irrigation and planting, leading to more sustainable farming practices.
Practical Recommendations for Implementing Sensors in Robotics
For those looking to implement sensor integration in their robotic systems, here are some actionable recommendations:
Assess Your Needs: Identify the specific tasks and environments your robots will operate in. This assessment will guide the selection of the most suitable sensors for your application.
Choose Quality Sensors: Invest in high-quality sensors to ensure reliability and longevity. For example, using industrial-grade proximity sensors in manufacturing robots can reduce maintenance costs in the long run.
Integrate Wisely: When integrating sensors into robotic systems, consider their compatibility. Ensure that the sensors can communicate effectively with the robot’s control system.
Test and Iterate: After integration, conduct thorough testing to identify any issues and optimize performance. Gather data from the sensors to make necessary adjustments and improvements over time.
Stay Updated: The field of robotics is constantly evolving. Stay informed about the latest advancements in sensor technologies and how they can be applied to improve your robotic systems.
By following these guidelines, organizations can effectively leverage sensor technology to enhance their robotic solutions.
Embrace the Future of Robotics with Sensors
The integration of sensors in robotic systems is not just a trend; it is a fundamental shift that enables advanced functionalities and applications. As we continue to innovate and incorporate new technologies, the importance of sensors will only grow. By understanding their capabilities and potential, businesses can harness the power of robotics to improve efficiency, safety, and decision-making across various sectors.
In conclusion, sensor integration plays a vital role in advancing robotic technology. As we have seen, the combination of different sensor types enhances a robot's ability to interact with its environment, making it smarter and more efficient. Embracing this technology will pave the way for the future of robotics, marked by greater innovation and integration across multiple industries.